The three main materials used for our bearing seals are Nitrile rubber, Polyacrylate, and Flouroelastomer. Nitrile rubber is the standard seal material used in our bearings. More demanding conditions may require the use of other seal materials. Table 1 shows some pros and cons of three common seal materials.
Our standard bearings are used in a wide variety of application conditions, each requiring a proper grease fill to optimize bearing life. As the life of the bearing is impacted greatly by grease life, how do we obtain more grease life? The answer to this question may be to add more grease.
Perhaps the next question would be how much grease to add. Can we fill the bearing up 100%? This would not be a practical solution, because once the bearing rotates, the rolling elements and cage would force their way through the grease and cause it to displace somewhere - typically out through the seals or shields. So, the initial fill of grease is not as important as the resultant fill.
For slower speed applications grease fills from 50% to 70% may be provided. In contrast, high speed applications often require a smaller grease fill, perhaps 15% to 20%. In high speed applications, excessive heat generation and grease churning due to the extreme dynamic forces experienced by the bearing can actually cause bearing failure when grease fill is too high.
Although bearing surfaces appear to be very smooth, a microscopic view shows that these surfaces can be, in actuality, very jagged. An illustration of these jagged features can be seen in Figure 1. Bearing wear is the result of these jagged surface peaks impacting each other during operation. With this in mind, the goal is to minimize these impacts by allowing these edges to ride on a layer of lubrication.
Three types of surface contact are possible; boundary, mixed, and full-film. Illustrations of these different types of contacts are shown in Figure 2. Boundary contact is characterized by a predominant surface-to-surface interface between the rolling element and the raceway. Under a boundary contact condition, excessive wear occurs rapidly and bearing life is often undesirable. Mixed contact is characterized by a combination of a lubricant film and surface-to-surface interface between the rolling element and the raceway. Under a mixed contact condition, there is some wear and bearing life will be reduced. Full-film contact is characterized by a predominant lubricant film interface between the rolling element and the raceway. Under a full-film contact condition, an optimal film layer exists and bearing life is maximized.
Again, the goal is to achieve a full-film lubrication condition. This is accomplished by choosing the proper lubricant for the application. Bearing load, speed, and operating temperature are factors that must be considered when choosing the proper lubricant.
TOP
What is radial clearance and when should different clearances be used?
by Mike Mortensen - Director of Engineering RBI-USA
Internal clearance is defined as the total distance that the inner ring and outer ring can be displaced in relation to each other. It can be expressed in terms of both the axial and the radial direction. Typically, the internal clearance for radial ball bearings is specified in the radial direction. Figure 1 shows a diagram of what internal clearance is. Different applications may require different clearances to accommodate a variety of operational conditions. Generally, the clearance after mounting and during operation should be close to zero. Therefore, it is important to know the application conditions in order to know how much clearance will be removed during operation.
Tight clearances are often used to accommodate applications that involve heavy shock loads and require minimal noise/vibration. If the internal clearance is reduced too much, many complications may occur. The bearing may seize up, the bearing may generate too much heat, the bearing may not tolerate tight press fits, and the bearing may not be able to handle the effects of thermal expansion.
Loose clearances are often used to accommodate applications that involve tight shaft/housing fits, thermal expansion of components, and possible mounting misalignment. If the internal clearance is too high, a couple of complications may occur. There may be excessive noise/vibrations as well as too much play during operation.
Again, the goal is ensure that the clearance after mounting and during operation is close to zero. If the clearance during operation is negative, a preload condition will occur and the bearing life will be greatly reduced. If the clearance during operation is too high, there can be excessive play that may permit the bearing to vibrate or be noisy during operation. It is better to have a little extra clearance than to have a preload condition.
Figure 1 . Diagram showing radial and axial clearance.
TOP
What Stainless Steel is used in RBI housings?
by Mike Mortensen - Director of Engineering RBI-USA
AISI 304 is a stainless steel that is used in our stainless housing series. It is characterized by its chromium (18-20%) and nickel (8-10.5%) content. The higher chromium content contributes towards its oxidation and corrosion resistance. AISI 304 stainless steel is resistant to food acids, sterilizing solutions, organic chemicals, many inorganic chemicals, and most oxidizing acids. These characteristics of 304 stainless steel have given it a niche market in the poultry and food processing industry where the housings are very likely to be exposed to water, food, and cleansing agents.
Cast iron housings are painted or plated in order to prevent corrosion. If the paint or plating is scratched or chipped, the housing is exposed and corrosion can easily occur. By using stainless steel, there is no need to paint or plate the surface of the housing and therefore, scratches do not affect the performance or appearance of the housing. The thermal and mechanical properties such as strength or heat resistance are not compromised by choosing to stainless steel over cast iron. The sacrifice is that stainless steel is a bit more expensive.
TOP
What material does RBI use for plastic housings?
by Mike Mortensen - Director of Engineering RBI-USA
The material that RBI uses for its plastic housing series is PBT ( Polybutylene terephthalate ). PBT is very common plastic that can be found in automotive, industrial, and electronic markets. The greatest value that it brings to the bearing industry is that it is resistant to corrosion as well a wide variety of chemicals and solvents. PBT allows our housings to be washed downed with various cleaning solutions as well as exposed to water and moisture.
As an engineering plastic, PBT offers considerable strength and stiffness despite being light weight. This material's good dimensional and thermal stability allow our plastic housings to resist distortion at elevated temperatures. Again, PBT is a viable material option for housings in applications where resistance to corrosion, moisture, and chemicals is a must.
TOP
What is black oxide and how is it applied?
by Brian Kleszyk - Applications Engineer RBI-USA
When parts undergo a black oxide treatment, the result is jet black color, commonly seen in firearms. A black oxide treatment is different than other surface coating or plating processes in that it is chemical surface treatment. The process can be applied to a variety of ferrous metals and alloys as well as copper, brass, and bronze.
There is both a hot and cold black oxide process. At elevated temperatures, the hot process uses various chemical mixtures that consist of caustic sodas, oxidizing salts, and other agents, which can vary from vendor to vendor. This mixture then chemically reacts with the iron on the surface of the part, converting it to the black oxide of iron. The volume of this new black oxide of iron is the same as the original iron. The hot blackening process is very hazardous, and must be performed with extreme caution due to the high heat required and caustic nature of the mixture.
Cold blackening process uses a different chemical mixture and does not require elevated temperatures. Because of this, the cold blackening process is not as hazardous. Although the chemical reaction in cold blackening results in the same black surface appearance, it is typically not as effective or as permanent as the surface finish resulting from a hot blackening process.
TOP
Why would black oxide finish be used?
by Brian Kleszyk - Applications Engineer RBI-USA
There are many advantages to using a black oxide finish for metal parts. Black oxide is a chemical surface treatment; not a coating or plating process where material is added to the surface that may eventually chip or peel away. Because black oxide is a conversion process, it allows for dimensional and surface finish stability.
Corrosion resistance is marginally improved for surfaces that have been treated with black oxide. This may be attributed to the increased absorption of oils and waxes on a black oxide surface. If, however, corrosion resistance is critical, there are other processes or materials that should be considered instead of relying solely on a black oxide coating.
The biggest impact of black oxide is that the finish reduces glare, brightness, and reflection. This characteristic is very important in many military applications where stealth may be desired. Aside from reduced glare and brightness, black oxide also offers the aesthetic appeal of a black surface, which may be the primary reason that people prefer a black oxide finish.
TOP
Are there advantages to using ceramic balls?
by Mike Mortensen - Director of Engineering RBI-USA
An alternative material used for ball bearing balls is silicone nitride (Si 3 N 4 ). Silicone nitride balls have many advantages over the standard 52100 chrome steel balls. Ceramic balls possess a variety of characteristics that contribute towards improved wear resistance and performance.
Silicone nitride is a much harder material than steel, which translates into a higher load capacity. Silicone nitride is not as dense as steel, therefore there is less centrifugal force acting on the bearing ring, thus reducing wear. Silicone nitride balls typically have a much smoother surface finish and as a result, friction is reduced. The reduced friction reduces the amount of heat generated during operation, thereby decreasing the grease degradation during operation as well as allowing the bearing to operate at higher speeds. Ceramics, in general, are much more thermally stable than steel.
This behavior allows silicone nitride to retain its material properties at much higher temperatures than steel. Yet another benefit of using silicone nitride is its resistance to corrosion. Although silicone nitride balls have superior performance than steel ball, the cost is much higher. Despite the initial cost disadvantage, a growing number of customers dealing with specialized applications are investigating and requesting ceramic balls for their bearings.
TOP
How is the hardness of metals measured?
by Mike Mortensen - Director of Engineering RBI-USA
There is a wide variety of hardness test methods and scales that can be used when analyzing the hardness of a material. Common hardness test methods for metals include the Rockwell, Vickers, Brinell, and Knoop hardness tests.
During a hardness test, an indenter of specific shape (i.e. ball, cone, pyramid, etc.) is pressed into the testing surface with a specified load, resulting in a permanent indentation (See Figure 1). Features of the permanent indentation are then measured and translated into a hardness value. The indenter material, indenter shape, applied load, measured indent feature, and hardness range vary between the different hardness testing methodologies.
Every test method has its own advantages and disadvantages. Certain advantages of specific testing methods include minimal indentation size, minimal indentation depth, ease of measurement, applicable material hardness range, etc.
. 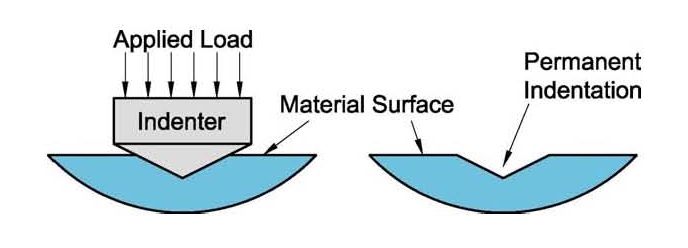
Figure 1 . Hardness test schematic showing the indenter creating a permanent indentation on a surface.
TOP
Which is a better cage material, nylon or pressed steel?
by Mike Mortensen - Director of Engineering RBI-USA
RBI typically supplies bearings with either nylon or pressed steel cages. Each material has its own advantages and disadvantages, making the optimal cage material vary from application to application. Table 1 draws a comparison between nylon and pressed steel cages over a variety of characteristics.
Table 1 . Comparisons between nylon and pressed steel cages.
NYLON |
CHARACTERISTIC |
PRESSED STEEL |
|
Availability |
X |
X |
Corrosion Resistance |
|
X |
Flexibility |
X |
Friction |
X |
Operational Noise |
|
Strength |
X |
Temperature Limit |
X |
TOP
How do the different hardness scales relate to each other?
by Mike Mortensen - Director of Engineering RBI-USA Several different scales exist to measure the hardness of a wide variety of manufacturing materials. Some scales are used to measure extremely hard materials, while other scales are used to measure softer materials such as rubber. Table 1 shows a comparison of a few of the more common hardness scales used to indicate the hardness of steel.
Table 1 . Comparison between commonly used hardness scales.
Rockwell C |
Vickers |
Brinell |
Diamond (Cone) |
Diamond (Pyramid) |
10mm Ball (Hardened) |
150 kgf |
10 kgf |
3,000 kgf |
68 |
940 |
- |
67 |
900 |
- |
66 |
865 |
- |
65 |
832 |
739 |
64 |
800 |
722 |
63 |
772 |
705 |
62 |
746 |
688 |
61 |
720 |
670 |
60 |
697 |
654 |
59 |
674 |
634 |
58 |
653 |
615 |
57 |
633 |
595 |
56 |
613 |
577 |
55 |
595 |
560 |
54 |
577 |
543 |
53 |
560 |
525 |
52 |
544 |
512 |
51 |
528 |
496 |
50 |
513 |
481 |
49 |
498 |
469 |
48 |
484 |
455 |
47 |
471 |
443 |
46 |
458 |
432 |
45 |
446 |
421 |
44 |
434 |
409 |
43 |
423 |
400 |
42 |
412 |
390 |
41 |
402 |
381 |
40 |
392 |
371 |
TOP
Why do bearings heat up during operation?
by Mike Mortensen - Director of Engineering RBI-USA
As bearings operate in an application, they heat up due to internal and external sources. Friction is the main source for heat generation during operation. It occurs between the balls and the cages as well as between the balls and the raceways. In sealed bearings, there is also frictional contact between the seals and the inner ring.
Another source of internal heat generation comes from the churning of the grease as the bearing rotates. The external sources of heat generation come from the operating conditions that are particular to the application. In some applications, heat from the housing or the shaft may conduct into the bearing. Other sources of heat could be from the environmental conditions of the application, such as heated air encountered in a furnace application or engine compartment.
TOP
What is the maximum temperature limit of RBI's standard steel bearings?
by Mike Mortensen - Director of Engineering RBI-USA
The maximum operating temperature for a bearing is based on the temperature limitations of the materials used in the bearing. Essentially, the material with the lowest temperature limit determines the highest temperature that the bearing can operate properly. Table 1 shows the approximate maximum useful temperature for a variety of bearing materials used in RBI's standard bearings. From the table, it can be seen that RBI's standard 52100 steel bearings are not recommended for continuous use in temperatures above 250 ° F.
Table 1 . Maximum useful temperature for bearing materials.
Bearing Component |
Material |
Maximum Useful Temperature |
Rings/Balls |
52100 Steel |
~250 ° F |
Cages |
Nylon 6/6 |
~230 ° F to ~250°F |
Pressed Steel |
~400°F to ~450°F |
Seals |
Buna N Rubber |
~250 ° F |
Lubricant |
Polyurea Grease |
~350 ° F |
TOP
Options that will allow bearings to withstand high temperatures
by Mike Mortensen - Director of Engineering RBI-USA
For bearing applications experiencing operating temperatures above 250 ° F , some extra cost features may improve bearing performance and life. Some bearing manufacturers offer heat stabilized 52100 steel that has improved dimensional stability at higher temperatures. Another material option for the bearing ring and ball material could be 440C stainless steel, which remains dimensionally stable up to 300° F. The most costly option would make use of ceramic ring and ball materials allow for extremely high operating temperatures that standard bearing steels cannot achieve.
It is advised that nylon cages should not be used for applications that experience operating temperatures above 230° F. A better option would be to use RBI's standard low carbon steel or 302 stainless for the cage material, which can withstand operating temperatures of up to 400° F. Shields are made from steels that are very similar to steels used form cages, thus the shield material is not much of a concern in regards to elevated operating temperatures. On the other hand, seal material choice is critical for elevated operating temperatures. Two options that are available are polyacrylate rubbers and flouroelastomers. Polyacrylate rubber can withstand operational temperatures up to 350° F, while flouroelastomers can withstand operational temperatures up to 400° F.
Aside from the various bearing materials, grease selection is critical for applications that exceed 250° F operating temperatures. Most bearing lubricants degrade when exposed to continuous elevated temperatures, and lose their ability to effectively lubricate the bearing. This may reduce bearing life significantly. This issue can be resolved by choosing fluorinated greases which are designed to withstand exposure to high temperatures.
TOP
What makes stainless 440C steel stainless?
by Mike Mortensen - Director of Engineering RBI-USA
The term “stainless” is used to describe materials that do not develop oxide layers or rust. This allows the products made from stainless steel to be used in applications where exposure to moisture is expected.
440C stainless steel contains approximately 16% to 18% chromium. When exposed to air, the chromium molecules react with the oxygen to produce a thin layer of chromium oxide, which stays on the metal surface. This process is called passivation and occurs quickly. Therefore, if the metal surface is scratched, a new chromium oxide layer develops immediately and the metal surface remains protected.
These oxide atoms are similar in size to the chrome atoms, allowing for them to be packed tightly with each other. By being tightly packed, the layer is very stable and cannot be penetrated by water. If water cannot reach the iron atoms, then rust corrosion will not occur.
TOP
What insert bearings does RBI make?
by Mike Mortensen - Director of Engineering RBI-USA
RBI offers a variety of insert bearings. The two types of mounting designs that RBI insert bearings use set screw mounting and eccentric locking collar mounting. The two types of outer ring designs are spherical and cylindrical. Spherical outer rings can be easily assembled with RBI housings. SER series bearings differ from the other series in that they come with snap rings. Table 1 shows the differences between the different RBI insert bearing series.
Table 1 . RBI Insert Bearing series.
Series |
Outer Ring |
Mounting Method |
Sealing Configuration |
SA |
Spherical |
Eccentric Locking Collar |
Trash Guard Seal |
CSA |
Cylindrical |
Eccentric Locking Collar |
Trash Guard Seal |
HC |
Spherical |
Eccentric Locking Collar |
Slinger + Rubber Seals |
CHC |
Cylindrical |
Eccentric Locking Collar |
Slinger + Rubber Seals |
SB |
Spherical |
Set Screw |
Trash Guard Seal |
CSB |
Cylindrical |
Set Screw |
Trash Guard Seal |
UC |
Spherical |
Set Screw |
Slinger + Rubber Seals |
CUC |
Cylindrical |
Set Screw |
Slinger + Rubber Seals |
UCX |
Spherical |
Set Screw |
Slinger + Rubber Seals |
SER |
Cylindrical |
Set Screw |
Slinger + Rubber Seals |
TOP
How should bearings be stored or handled?
by Mike Mortensen - Director of Engineering RBI-USA
It is important that bearings are stored and handled properly. Regardless of manufacturing quality, bearings that are stored or handled improperly run the risk of performing poorly when used.
Ideally, bearings are stored in a cool dry environment. If the bearings are stored in an environment that is too hot or cold, the lubricant’s physical characteristic may be adversely affected and the lubricant may not effectively lubricate the bearing during operation. If the environment is not dry enough, then the moisture in the air can cause the bearing steel to corrode. Often during packaging, the bearings are covered with a light rust preventative oil to prevent the corrosion from occurring. As with many precision components, it is critical that bearings are not exposed to any sort of dust or water.
Careful consideration must be made as to how the bearings are stored. It is advised that the bearing cartons should not be stacked high. If the cartons are stacked too high, the excessive weight may damage the packaging, which can lead to damaged bearings.
Often overlooked, the mishandling bearings can be severely detrimental their performance. Bearings should only be removed from the packaging when they are ready for mounting into the application. This limits the amount of contaminants that the bearings are exposed to. Bearings should not be touched with bare hands due to the moisture, oil, and salt on your skin. Often, bearings and other industrial components that are frequently handled with bare hands will show signs of corrosion in the shape of fingerprints. Bearings that have been rattled or dropped should not be used. Dropping or excessive rattling of the bearings can cause internal damage, which can lead to premature bearing failure.
TOP
How does rust form?
by Mike Mortensen - Director of Engineering RBI-USA
Rust corrosion is very detrimental to the operation of a bearing. For proper operation, the rolling surfaces of the bearing must be smooth and free of imperfections. Rust corrosion reduces the smoothness of the surface and strength of the material, leading to a reduction in the life of a bearing.
Iron, oxygen, and water are required for rust to form. Iron atoms will not actively react with oxygen in air molecules, but it will react with oxygen in water molecules. This is because oxygen atoms in the water are not paired together with one another and iron will only react with unpaired oxygen atoms. That is why water or moisture is required for rust to develop on a metal surface.
When a drop of water comes into contact with iron atoms a reaction occurs. The iron atoms readily release electrons and enter the water as positively charged iron ions. The released electrons flow through the metal and combine with the water and the oxygen within the water to produce hydroxide ions. The positively charged iron ions that are now present in the water react with these hydroxide ions and oxygen to produce iron oxide. Iron oxide is the reddish orange material that is commonly referred to as rust.
TOP
What is the importance of bearing ring chamfers?
by Mike Mortensen - Director of Engineering RBI-USA
It is important that bearings are mounted onto a shaft or into a housing properly. Even bearings made of the highest quality steel with adequate lubrication may fail quickly if it not installed properly. A key dimension affecting the mounting quality is the inner and outer ring chamfers. Figure 1 and Figure 2 shows how bearings are pressed onto shafts and/or into housings. If the bearing face is to be pressed flush against another surface, it is critical that the curvature of the shaft/housing be smaller than the curvature of the bearing edge (see Figure 3). If the bearing cannot seat properly, then it may become misaligned with the shaft/housing and possibly lead to undesirable bearing performance (see Figure 4).
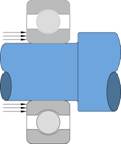
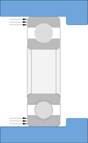
Figure 1 : Pressed onto shaft. Figure 2: Pressed into housing.
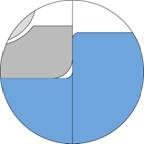
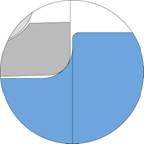
Figure 3: Seated Properly. Figure 4: Seated Improperly.
TOP
How are bearing ring chamfers specified?
by Mike Mortensen - Director of Engineering RBI-USA
There are two common methods of specifying bearing chamfers. One method is in terms of a minimum radius. The second method is in terms of a linear dimension in both the axial (through the bore) and radial (along the bearing face) direction. These linear dimensions may be accompanied by tolerances that specify the minimum and maximum values.
Figure 1 demonstrates the different ways in which chamfers are specified on drawings.
Figure 1: Chamfer radius specification.
TOP
What are the limitations of 440C stainless steel?
by Mike Mortensen - Director of Engineering RBI-USA
The most common material used in stainless steel bearings is 440C.
440C stainless steel has higher carbon content and can be heat treated to form a martensitic microstructure, leading to increased strength, hardness, and wear resistance over 300 series stainless steels. These qualities make heat treated 440C stainless steel suitable for bearings rings and rolling elements.
Despite these advantages, however, there are some drawbacks to using 440C. The strength and wear resistance of 440C stainless steel is less than that of standard 52100 bearing steel. Load ratings of bearings made from 440C stainless steel are typically about thirty percent less than load ratings of bearings made from 52100 steel. Although 440C exhibits significantly more corrosion resistance than 52100, it is still vulnerable to water mixtures containing salts and chlorine.
In fact, martensitic stainless steels tend to be less corrosion resistance than austenitic stainless steels found in the 300 series stainless steels (i.e. 302, 304, and 316). 440C stainless steel is magnetic, like 52100, whereas 300 series stainless steels are not. Due to these characteristics, it is important to factor in all application conditions before assuming that 440C stainless steel is appropriate.
TOP
What are some general guidelines regarding bearing fitting practice?
by Mike Mortensen - Director of Engineering RBI-USA
One thing that is just as important as choosing a good quality bearing, is deciding how to mount the bearing to the desired assembly. Although every application is unique, there are some general guidelines to use when deciding how to mount bearings.
The press fit should be applied to the ring that is rotating. For example, if the application requires the outer ring to rotate and the inner ring to remain stationary, then the press fit should be applied between the housing and outer ring.
Applications where heavy or shock loading exist typically require tighter press fits.
Tighter press fits result in an increase in rigidity, which is desirable for some applications
If the press fit is too tight, then clearance may be completely removed. This may result in deformed rolling elements/raceways, excessive heat generation, cracked rings, and reduced bearing life.
If the press fit is too loose, then the bearing ring may creep and damage either the shaft or housing bore.
Heat generation causes materials to expand. Different materials have different heat expansion coefficients which cause them to expand at different rates. This difference in heat expansion between the shaft, housing, and bearing materials will affect the shaft and housing fits.
TOP
How is the radial internal clearance of insert bearings specified?
by Mike Mortensen - Director of Engineering RBI-USA
Radial internal clearance ranges for insert bearings are specified in a manner that is very similar to ranges for deep groove ball bearings. See the table below for the various clearance ranges specified for insert bearings based on bore diamete
Nominal Bore
Diameter (mm) |
Radial Clearance (um) |
C2 |
C0 |
C3 |
C4 |
From |
To |
Min |
Max |
Min |
Max |
Min |
Max |
Min |
Max |
10 |
18 |
3 |
18 |
10 |
25 |
18 |
33 |
25 |
45 |
18 |
24 |
5 |
20 |
12 |
28 |
20 |
36 |
28 |
48 |
24 |
30 |
5 |
20 |
12 |
28 |
23 |
41 |
30 |
53 |
30 |
40 |
6 |
20 |
13 |
33 |
28 |
46 |
40 |
64 |
40 |
50 |
6 |
23 |
14 |
36 |
30 |
51 |
45 |
73 |
50 |
65 |
8 |
28 |
18 |
43 |
38 |
61 |
55 |
90 |
65 |
80 |
10 |
30 |
20 |
51 |
46 |
71 |
65 |
105 |
80 |
100 |
12 |
36 |
24 |
58 |
53 |
84 |
75 |
120 |
TOP
How important is seal drag?
by Brian Kleszyk - Applications Engineer RBI-USA
For certain applications the seal drag plays an important role in how well the bearing performs. Depending on the characteristics of the application, the bearing may specifically require light contact or heavy contact seals. The table below outlines the pros and cons of both configurations. RBI’s standard seals are light contact, but heavy contact is available.
Heavy Contact Seal |
Pros |
Cons |
-Less likely to experience grease purging
-More protective against debris & contamination
|
-Higher torque needed to turn bearing
-More heat generation
-Limited speed permitted |
Light Contact Seal |
Pros |
Cons |
-Lower torque needed to turn bearing
-Less heat generation
-Higher speed permitted |
-More likely to experience grease purging
-Less protective against debris & contamination |
TOP
The results that are attained using bearing life calculations are based on theoretically optimal conditions of bearing operations. Such optimal conditions include perfect fitting conditions, perfect shaft alignment, clean environment, stable temperatures, evenly distributed grease, and consistent loading.
It is unlikely that all application conditions are optimal. For example, the fitting conditions might be such that the internal clearance of the bearing is more than the fluid film thickness and would lead to some chattering of the rolling elements. Another example would be that there is a small degree of shaft deflection and, therefore, bearing operates with a slight misalignment. The fact that most application conditions are far from optimal suggests that bearing life calculation results are only estimates.